Problemi e soluzioni. I primi sono storici, radicati, complessi da risolvere. Nascono da epoche costruttive molto diverse da quella attuale, che pur sconta più di una criticità, ma anche da trascuratezze, inconsapevolezze, miopie. Le seconde arrivano dalla ricerca, dallo sviluppo, dall’innovazione, dalla profondità di un impegno, nel progetto e sul cantiere, che deve essere a tutto campo, senza lasciare indietro nessun dettaglio, sia nella “materia plasmata” sia nell’intero processo della sua trasformazione, da materiale inerte a viva “pietra” costruttiva.
Negli articoli che seguono del nostro percorso di divulgazione tecnico-culturale realizzato insieme al network di Concretezza parleremo proprio di problemi – segnatamente i degradi del calcestruzzo – e di soluzioni, nel campo del miglioramento del calcestruzzo, in generale, e in una sua declinazione particolare e molto avanzata quale è Microbeton HTE, un prodotto fibrorinforzato che può davvero rivoluzionare l’approccio alla protezione dai sismi nelle costruzioni. Un aspetto metodologico da sottolineare: le soluzioni accennate trovano forza nel fatto che vanno alla radice del problema, ovvero la porosità del materiale e il suo lasciare le porte aperte all’ingresso di agenti che, presto o tardi, lo danneggeranno. Il punto cruciale è la protezione totale, l’impermeabilità a qualsiasi ingresso, liquido o aeriforme che sia. È in questo concetto che nasce la durabilità.
I contenuti che andremo a illustrare trovano origine nel ciclo di webinar dal titolo “Egregio Calcestruzzo”, che prima dell’estate l’Istituto Italiano per il Calcestruzzo ha messo online in collaborazione con gli Ordini degli Ingegneri del Friuli Venezia Giulia, del Consiglio Nazionale degli Ingegneri e della nostra testata (tra i protagonisti, anche l’Anas).
Per ulteriori focus sempre tratti da questi intensi momenti “di formazione e informazione”, per dirla con l’ideatore della rassegna e presidente IIC Silvio Cocco, rimandiamo agli scorsi numeri di leStrade Giugno e leStrade Luglio.
Vi è la porosità del calcestruzzo all’origine di ogni tipologia di degrado
“Solo in occasione di grandi disgrazie, solo davanti ai morti e solo per qualche tempo, l’opinione pubblica si scatena e le autorità si muovono tutte in cerca di una vana gloria del momento. Poi tutto si assopisce. Come per magia è stato sufficiente quel momento, quell’effimera gloria di aver alzato i toni, di essersi messi in mostra, di essersi fatti notare. Poi si ritorna al silenzio, nel silenzio più profondo, il più piccolo brusio può dare fastidio. Attendiamo nel silenzio la prossima disgrazia…”. Citando questa riflessione di Silvio Cocco, presidente IIC, si è aperto l’intervento a cura di Valeria Campioni, direttore tecnico della Fondazione Istituto Italiano per il Calcestruzzo, che ha approfondito la questione dei degradi, centrale nel mondo delle costruzioni quantomeno dal terremoto dell’Aquila del 2009, passando per i noti crolli di ponti del decennio successivo fino all’immane tragedia del crollo del ponte sul Polcevera, a Genova.
Emblematiche le immagini mostrate da Campioni e provenienti da una raccolta del professor Pietro Pederferri, in cui per esempio nel giro di poco tempo la corrosione per carbonatazione è riuscita a “divorare” i copriferro, lasciando le armature in bella vista… “Queste immagini denotano seri problemi di ‘comunicabilità’ tra ferro e calcestruzzo, materiali che invece sono del tutto armonici dal punto di vista della solidità costruttiva. Come si è arrivati a questo punto? Se non vogliamo pensare al dolo, possiamo dire quantomeno che c’è stata tanta inconsapevolezza. Nasce anche e soprattutto da qui il nostro sforzo nel sensibilizzare gli specialisti sulle corrette modalità da mettere in atto per progettare e mettere in opera il calcestruzzo”. Il punto di partenza è la conoscenza del calcestruzzo, quindi una sua corretta progettazione. Uno studio degli anni Settanta citato da Campioni già metteva in evidenza come le cause del degrado del calcestruzzo fossero nel 42% dei casi “tecnologiche” e nel 22% “costruttive”. Un buon 64%, dunque, legate
alla non corretta progettazione, produzione, qualifica, messa in opera e controllo del materiale! Senza cioè attivare, per esempio, adeguati presidi dei getti. “Il degrado – ha aggiunto Campioni – è esattamente il contrario della durabilità, quella che trova origine in un concetto: il calcestruzzo che progetto deve mantenere tutte le caratteristiche progettate nel tempo. E deve essere resistente, in tutte le classi di esposizione”. Le cause del degrado, ha proseguito la relatrice, possono essere interne (cattiva progettazione, non corretta posa in opera, inadeguata stagionatura, e via dicendo) o esterne (di tipo meccanico, fisico, chimico, ovvero da tutto quanto deriva dall’azione dell’ambiente o dell’uomo).
Sul piano strettamente tecnico, su questa strada progettuale e costruttiva che porta alla durabilità, diventa cruciale non modificare il rapporto acqua-cemento: uno degli obiettivi che concorrono al conseguimento del macro-obiettivo, ovvero fare sì che il calcestruzzo non presenti porosità. “Se il calcestruzzo è poroso la CO2 vi entra, trovandovi la calce libera, ed è questo l’inizio del processo che porterà alla corrosione per carbonatazione. In quel calcestruzzo dove la CO2 non arriva avrò invece un ambiente ideale alla preservazione dell’acciaio, che non verrà così aggredito né dalla CO2 né dall’umidità. Man mano che la CO2 entra in una struttura porosa automaticamente il Ph della matrice cementizia diminuisce, quando supera la soglia limite del Ph 9, allora il processo subisce un’accelerazione che porterà la struttura a indebolirsi e il ferro ad arrugginirsi”. La chiave dunque è l’eliminazione o la riduzione delle porosità. “Per ridurle bisogna o aumentare il copriferro, o applicare un passivante sulle armature. Oppure ridurre il rapporto acqua-cemento: è questa la via, forse più complessa, ma sicuramente più produttiva”. Un calcestruzzo durevole può impiegare anche un decennio per raggiungere 10 mm di carbonatazione. In un calcestruzzo poroso e dunque non durevole, il degrado è invece molto rapido. Aumentare il copriferro in certi casi significa soltanto dilazionare nel tempo il problema, occorre invece “andare sul calcestruzzo”, ovvero progettare e produrre calcestruzzi impermeabili e dunque sicuramente non porosi.
Lo stesso approccio vale per il contrasto alla carbonatazione così come alle aggressioni dei cloruri, che sono solo ancora più veloci e puntuali: occorre agire sul corretto rapporto acqua-cemento e diminuire le porosità.
E lo stesso vale per le classi di esposizione ai cicli gelo-disgelo: se il calcestruzzo è impermeabile nemmeno il ghiaccio può entrare, e quindi non può espandere e nemmeno fessurare. Men che meno i sali disgelanti (“Sul ponte di Annone, crollato nel 2017, le armature erano sparite, le barre non c’erano più…”).
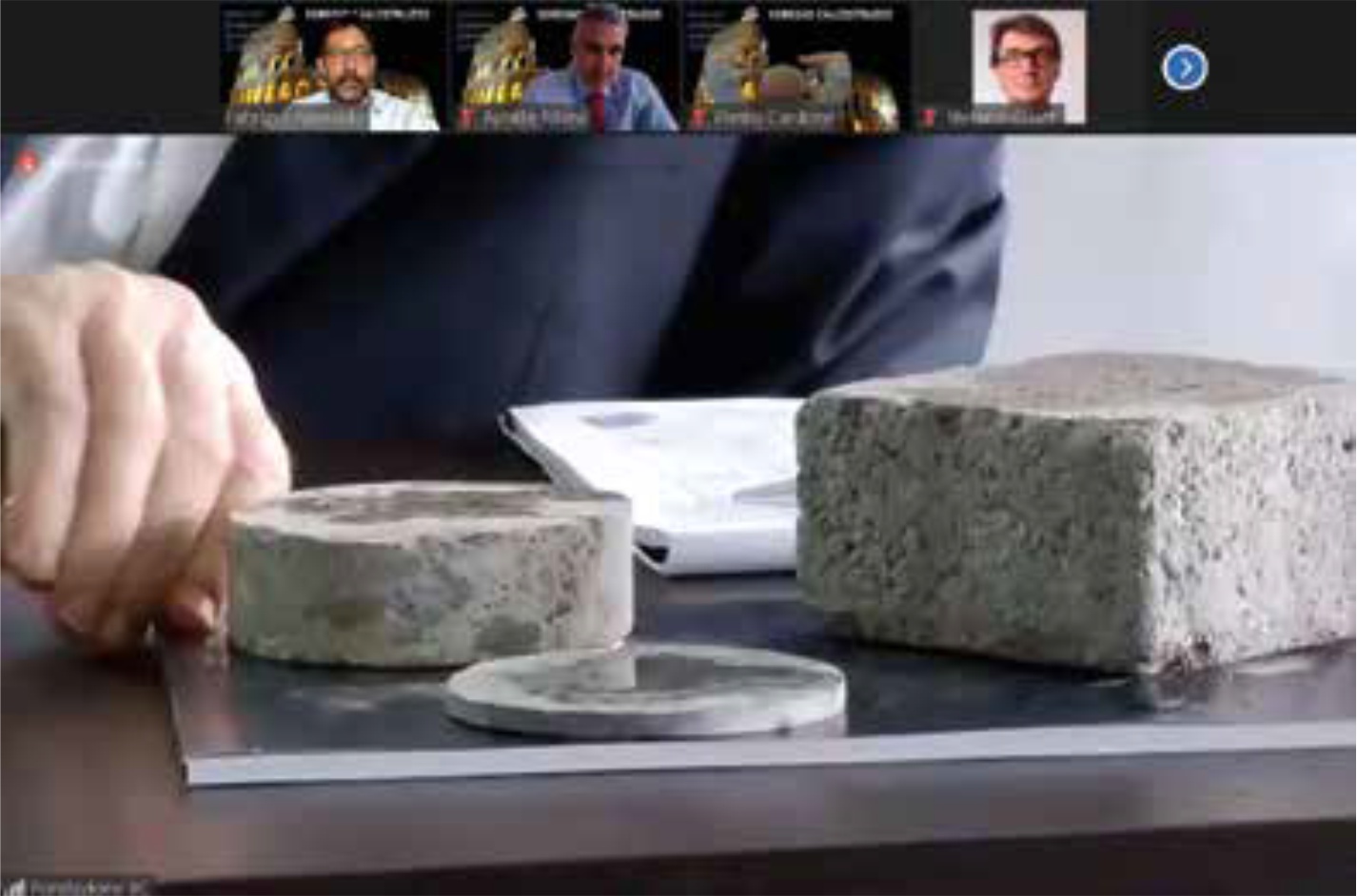
Scudo impermeabile per lo scudiero del ferro
Dal problema alla soluzione: un adeguato copriferro, il cemento idoneo, un basso rapporto acqua-cemento… ma soprattutto una soluzione che potesse rendere il calcestruzzo davvero assolutamente impermeabile, una soluzione, frutto della ricerca dell’Istituto Italiano per il Calcestruzzo, che ha trovato origine nel fatto che nei contesti costruttivi attuali difficile, o troppo oneroso, reperire quel cemento pozzolanico capace di non rendere più disponibile la calce libera alla carbonatazione. “Il compound che abbiamo sviluppato – ha concluso Campioni – garantisce un basso rapporto acqua-cemento, un’adeguata lavorabilità che eviti l’aggiunta di acqua, un’adeguata consistenza dell’impasto, una corretta compattazione del calcestruzzo. Ma soprattutto elimina le porosità e i vuoti, rendendo il calcestruzzo impermeabile”. Ulteriormente nel merito è poi entrato Silvio Cocco: “L’idea dell’Aeternum, questo il nome del nostro compound, è arrivata osservando i materiali della Roma Antica, in cui abbiamo notato l’assenza di calce benché le costruzioni romane fossero realizzate con calce idrata e pozzolana. Cosa è successo alla calce? Semplicemente, ha fatto reazione con la pozzolana. Anche nel cemento contemporaneo via è della calce libera ed è proprio questa che, dall’incontro nefasto con la CO2 che entra nelle porosità, genera quel carbonato di calcio che, abbassando Ph, abbassa il livello di protezione del calcestruzzo sul ferro.
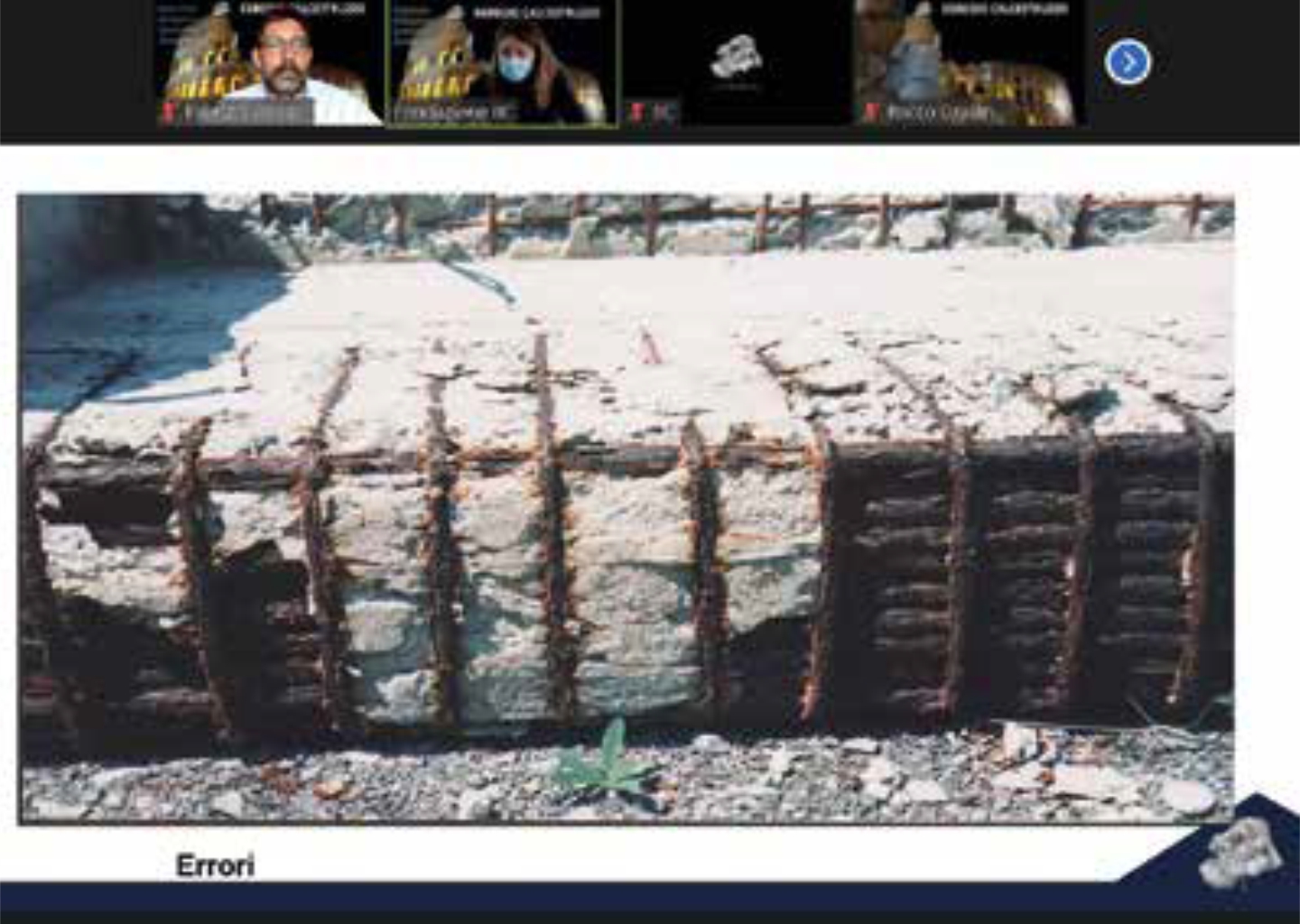
Il matrimonio tra calcestruzzo e ferro sarebbe infatti di per sé ideale, perché entrambi questi materiali hanno sì il medesimo coefficiente di dilatazione, ma il calcestruzzo ha un Ph che protegge il ferro dall’aggressione acida, annullando l’azione di ogni agente che bussi alla porta…”. Già, il calcestruzzo è lo scudiero del ferro, solo che per svolgere bene il proprio compito deve avere uno… scudo adeguato. “Ci siamo chiesti, in prima battuta, come fosse possibile eliminare la calce dal calcestruzzo, togliendo dunque di torno il principale agente del processo che porta alla carbonatazione. Lavorando su questa idea, abbiamo sviluppato un compound che poi si è rivelato eccezionale anche per garantire la totale impermeabilità del materiale. Già, un compound: un insieme di additivi capaci di combattere alcune precarietà del calcestruzzo. Dovevano introdurre, innanzitutto, un elemento reattivo che catturasse la calce: no, non la pozzolana oggi troppo costosa e reperibile solo in poche località, bensì delle silici reattive che provengono dalla lavorazione dell’acciaio, silicafumi, fumi di silice, che hanno subito la fusione totale e il raffreddamento rapido, e presentano un’altissima reattività con la calce libera. All’inizio si trattava di un prodotto microlecolare, poi abbiamo puntato anche su una soluzione ancora più nobile ed efficace: nanomolecole di silice. Da un mix dei due prodotti abbiamo ottenuto il risultato atteso: catturare tutta la calce libera immediata e sviluppata in un processo di più mesi. Avevamo raggiunto lo stesso risultato dei Romani, ma senza pozzolana! Eliminando la calce nel calcestruzzo, ogni molecola di CO2 che fosse entrata sarebbe stata subito disinnescata…”. Ma la ricerca, che ha portato allo sviluppo del compound Aeternum, non si è fermata certo qui. Ha concluso Cocco: “Per ridurre il rapporto acqua-cemento, riducendo le porosità, abbiamo introdotto nel compound un tensioattivo molto potente che fornisse anche una bagnabililtà dell’acqua elevatissima. Quindi abbiamo aggiunto un iperfluidificante in polvere di ultima generazione, nonché degli espansivi per evitare eventuali microritiri, un incrementatore chimico delle resistenze e un impermeabilizzante di massa. Ecco il nostro compound: un insieme di più additivi presenti in maniera bilanciata e collaboranti tra loro, un equilibrio perfetto. L’abbiamo usato nelle pavimentazioni industriali, sui ponti, nei conci delle gallerie. Grazie all’Aeternum il calcestruzzo diventa impermeabile all’acqua e all’aria e quindi durevole”.
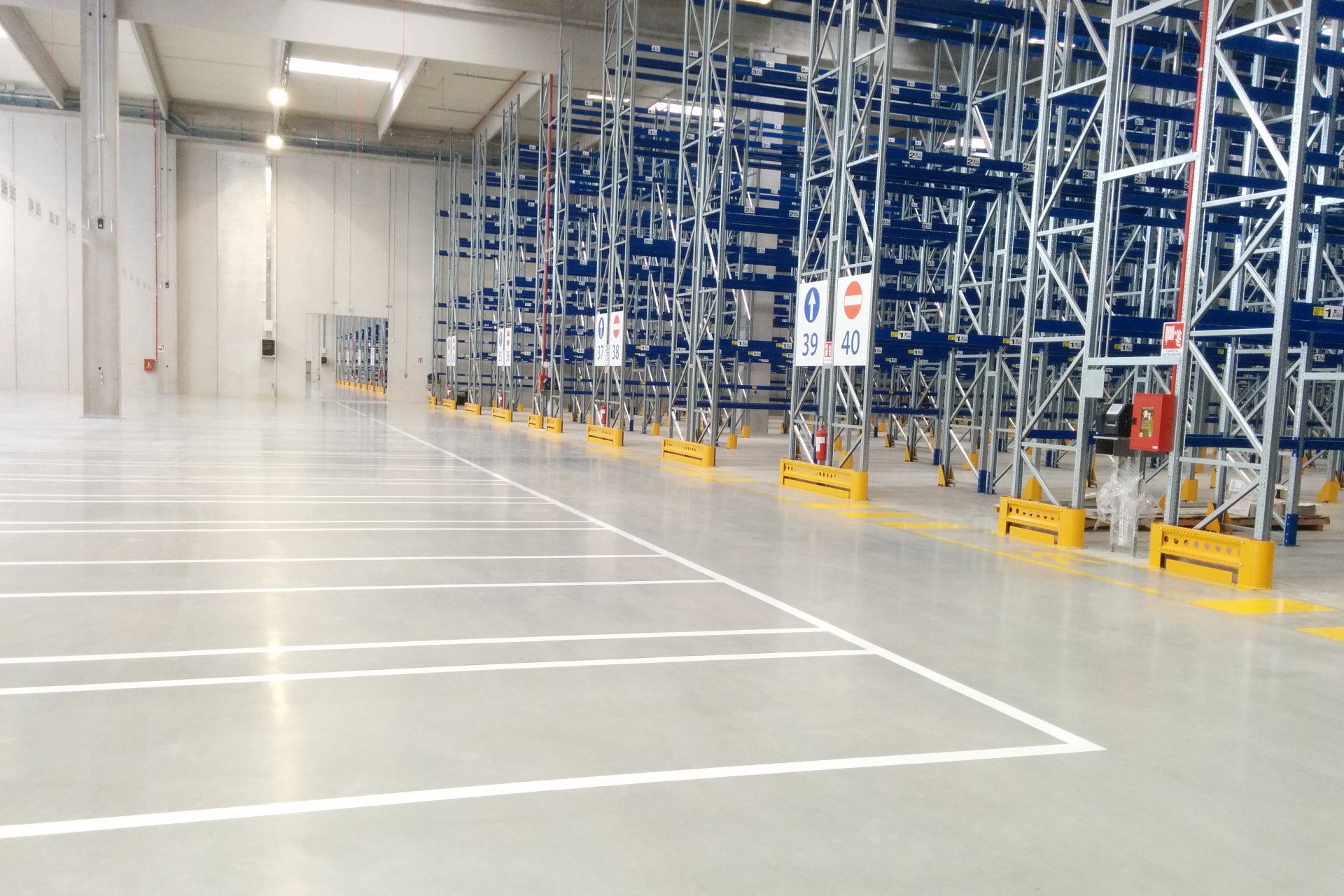
Micro-calcestruzzi con fibre e incamiciatura innovativa
Rocco Gravinese, ingegnere strutturista, ha concluso il terzo modulo del webinar “Egregio Calcestruzzo” con un focus sui micro-calcestruzzi Microbeton HTE, una delle ultime novità materiche sviluppate dall’Istituto Italiano per il Calcestruzzo di cui in altre occasioni, su questa rivista, abbiamo parlato. I micro-calcestruzzi – ha esordito Gravinese – nascono dall’esigenza di intervenire sul realizzato, sulla messa in sicurezza un parco edilizio che risale agli anni dal secondo Dopoguerra agli anni Ottanta presentando tutti i difetti tipici di calcestruzzo molto porosi e dunque spesso disgregati con ossidazione dei ferri di armatura. Il primo problema è dunque il risanamento materico, un’alternativa alla demolizione e ricostruzione. Si tratta, come è noto, di costruzioni realizzate sulla base di normative datate, “che consideravano in maniera inadeguata, per esempio, le sollecitazioni di origine sismica, non rispettando nemmeno i requisiti richiesti dalla normativa in termini di resistenza al taglio o duttilità, e portando alla realizzazione di nodi travi-colonna particolarmente deboli”. Per poter intervenire efficacemente in questo contesto problematico – ha riferito Gravinese – ci viene in aiuto un nuovo materiale, Microbeton HTE, dalle elevatissime resistenze a compressione, nonché, essendo additivato con fibre, anche con il vantaggio di presentare un’ottima resistenza a trazione.
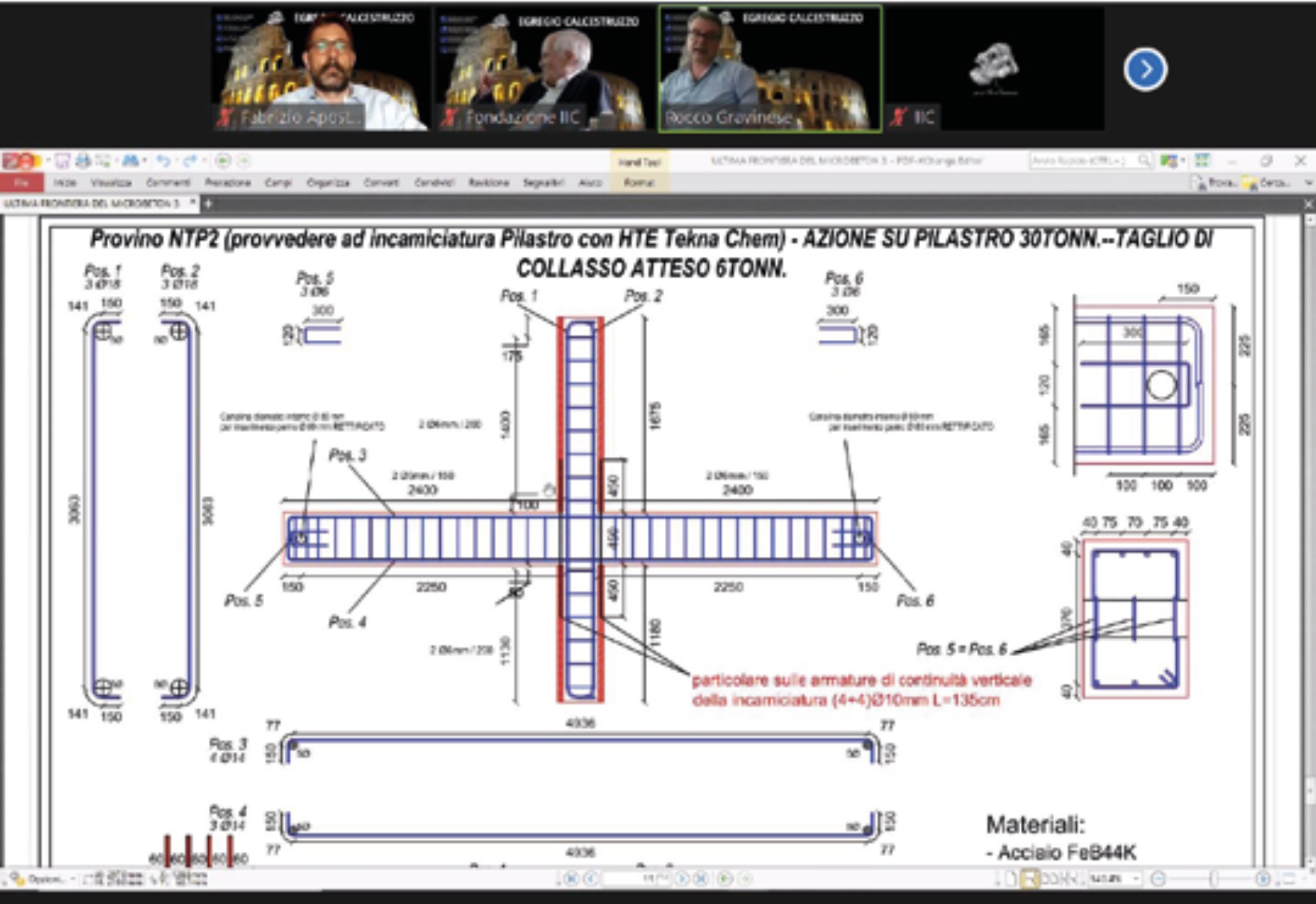
Ma sintetizziamo schematicamente, qui di seguito, le caratteristiche di questo micro-calcestruzzo:
- Resistenza a compressione a 28 gg: 150 Mpa
- Resistenza a trazione a 28 gg: 8,5 MPa
- Resistenza a flesso-trazione a 28 gg: 38 MPa
- Resistenza a taglio a 28 gg: 16 MPa
- Modulo elastico: 38 GPa
- Energia di frattura: 32.500 N/m
- Ritiro endogeno < 0,05%
- Profondità di carbonatazione: nulla (impenetrabile sia all’aria che all’acqua)
- Adesione al supporto su calcestruzzo: > 2,4 MPa.
Queste caratteristiche rendono particolarmente interessante e vantaggiosa la strategia di risanamento materico e di rinforzo dei pilastri e dei piloni esistenti di c.a. con la tecnica della camicia in Microbeton HTE. L’ incamiciatura tradizionale prevede infatti:
- Rimozione del cls ammalorato, in genere la rimozione di uno strato di circa 3 cm;
- Spazzolatura dei ferri di armatura corrosi, successiva applicazione di sostanze protettive dei ferri di armatura residuati alla pulizia;
- Montaggio di ferri di armatura pertinenti al ringrosso del pilastro;
- Montaggio di connettori metallici per rendere solidale il rivestimento di nuovo impianto (jacket) al nucleo del pilastro preesistente (core);
- Applicazione di resina a lentissima presa per incollaggio del nuovo cls (jacket) al vecchio supporto di cls preesistente (core);
- Montaggio delle casseforme e successivo getto di cls (jacket);
- Infine, realizzazione di ringrosso del pilastro di circa 15 cm su ciascun lato con sensibile aumento sia della massa che della rigidezza e quindi della sollecitazionesismica agente sul pilastro consolidato.
L’incamiciatura innovativa con Microbeton HTE prevede invece:
- Rimozione del cls ammalorato, in genere la rimozione di uno strato di circa 3 cm di cls;
- Spazzolatura dei ferri di armatura corrosi;
- Montaggio dei ferri di ancoraggio ai nodi e di lamiere di placcaggio al piede e in testa al pilastro;
- Montaggio di casseforme contenitive a perimetro del nuovo rivestimento in HTE e successiva iniezione di micro-calcestruzzo micro armato per formazione della nuova incamiciatura;
- Infine, realizzazione di ringrosso del pilastro di circa
3 cm su ciascun lato con trascurabile aumento sia della massa che della rigidezza e quindi della sollecitazione sismica agente sul pilastro consolidato.
“Il pilastro incamiciato con Microbeton HTE – ha concluso Gravinese – oltre a essere perfettamente risanato e protetto dal degrado materico, risulta essere molto più resistente e localmente più duttile (rotazione di corda in zona critica nel pilastro incamiciato sensibilmente aumentata rispetto al pilastro originario non degradato).
Tutto ciò è di particolare interesse nel caso di piloni e pilastri avente schema a mensola che oltre al risanamento materico necessitano di adeguamento e/o miglioramento sismico. Ancora più interessanti sono i risultati ottenibili nel caso di pilastri appartenenti a telai che presentano il tipico schema di Trave Forte E Pilastro Debole dove la crisi della struttura soggetta a sollecitazioni sismiche avviene per formazione di cerniera plastica nel pilastro. In detti telai, l’incamiciatura dei pilastri con Microbeton HTE e il placcaggio dei nodi trave-pilastro inibisce la formazione di cerniere plastiche nel pilastro e/o rottura a taglio del nodo e promuove la formazione di cerniere plastiche nelle travi. In sintesi, nei telai di c.a. si promuove l’attivazione di uno schema tipicamente antisismico ossia Pilastro Forte E Trave Debole con sensibile miglioramento della duttilità e della resistenza della struttura rispetto alle sollecitazioni di origini sismiche”.
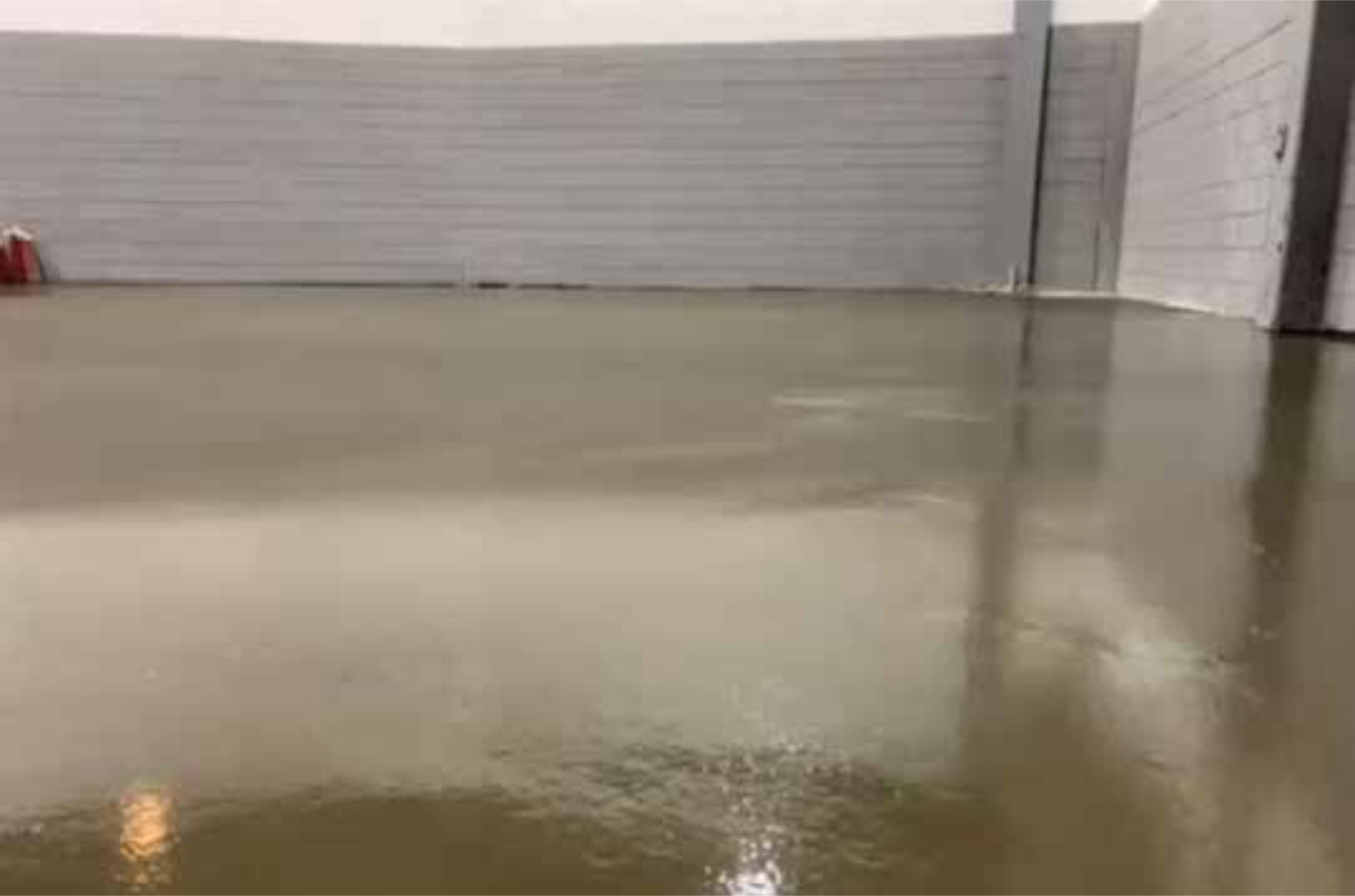
A cura di leStrade
in collaborazione con Istituto Italiano per il Calcestruzzo – Fondazione per la Ricerca e gli Studi sul Calcestruzzo